Case Study
STAC INTEGRATES ZERO PRESSURE ACCUMULATION CAPABILITIES WITHIN CAP GROUP FOR INCREASED EFFICIENCY
The CAP Group reached out to Stac for their expertise to design, integrate and install a customized zero pressure accumulation conveyor solution to increase speed, safety and efficiency within their facility while keeping ease of installation and maintenance top of mind.

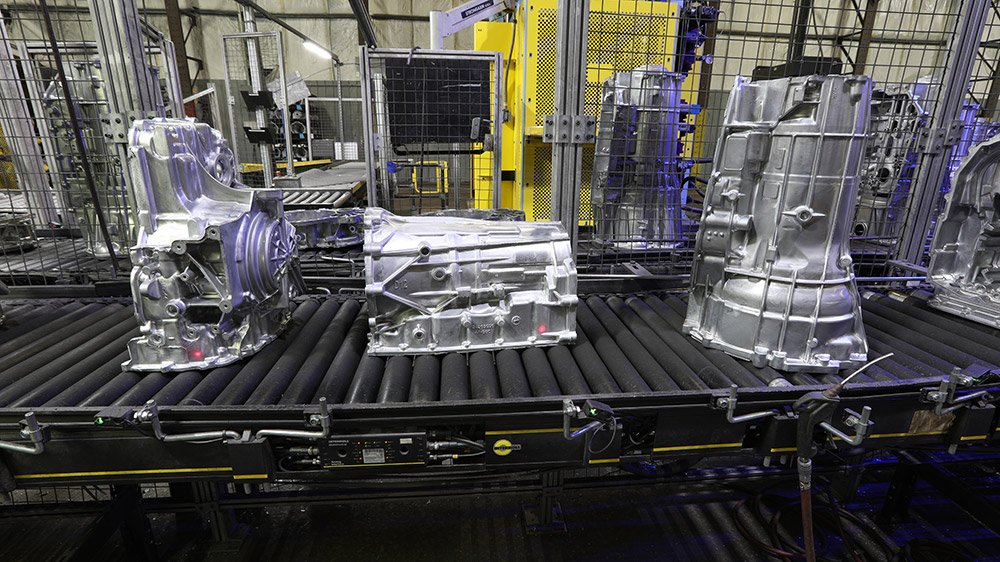
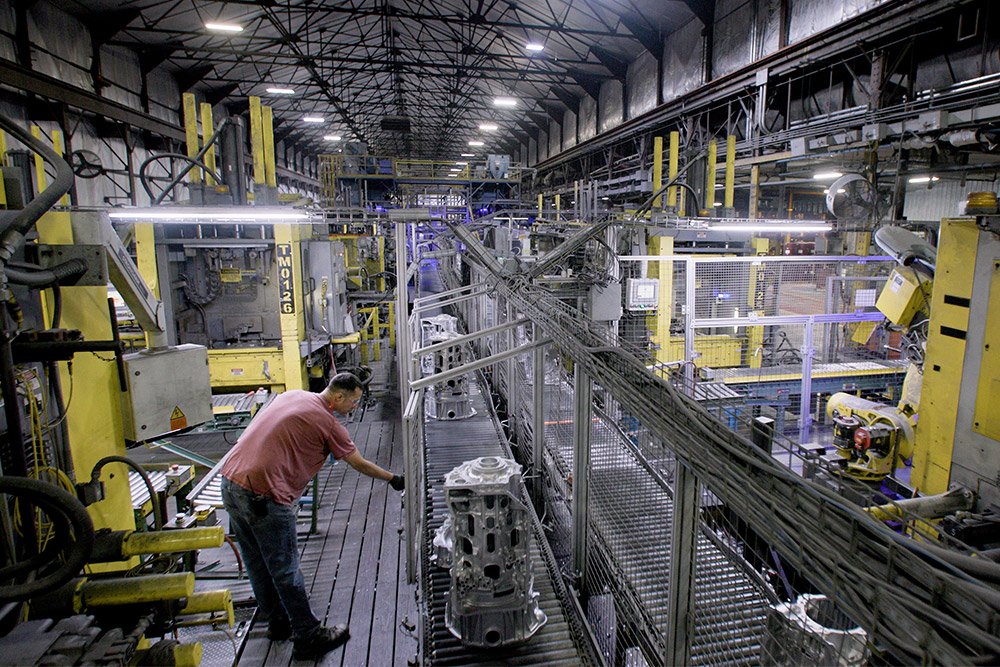
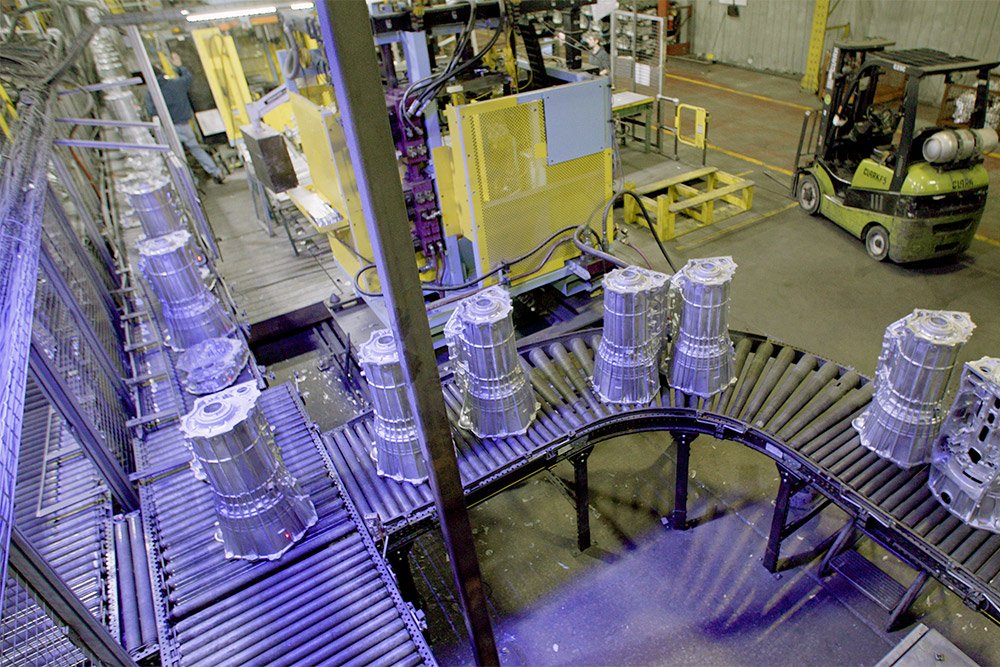
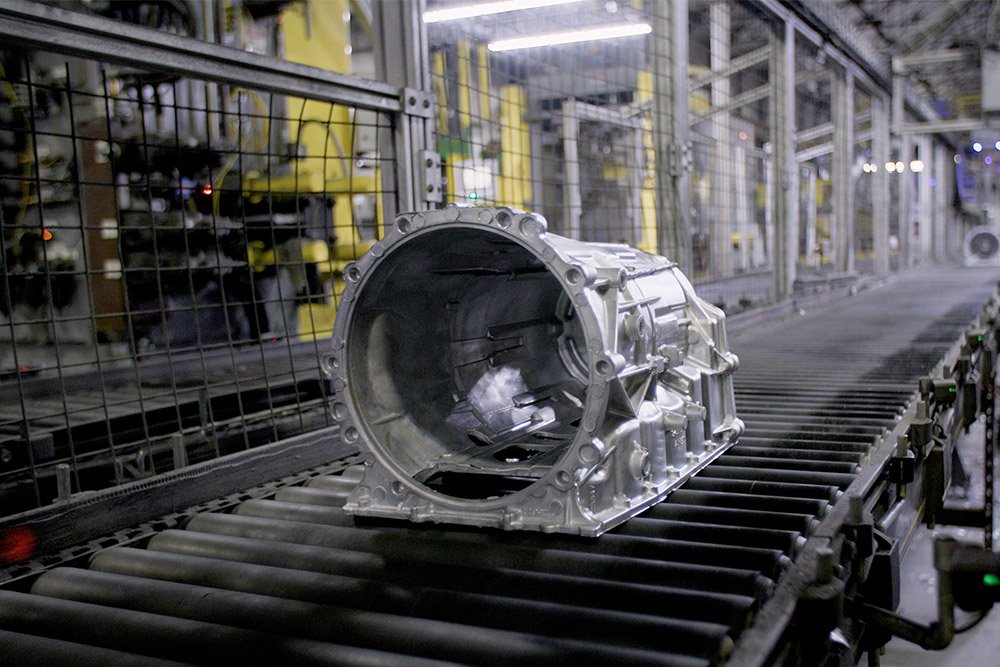
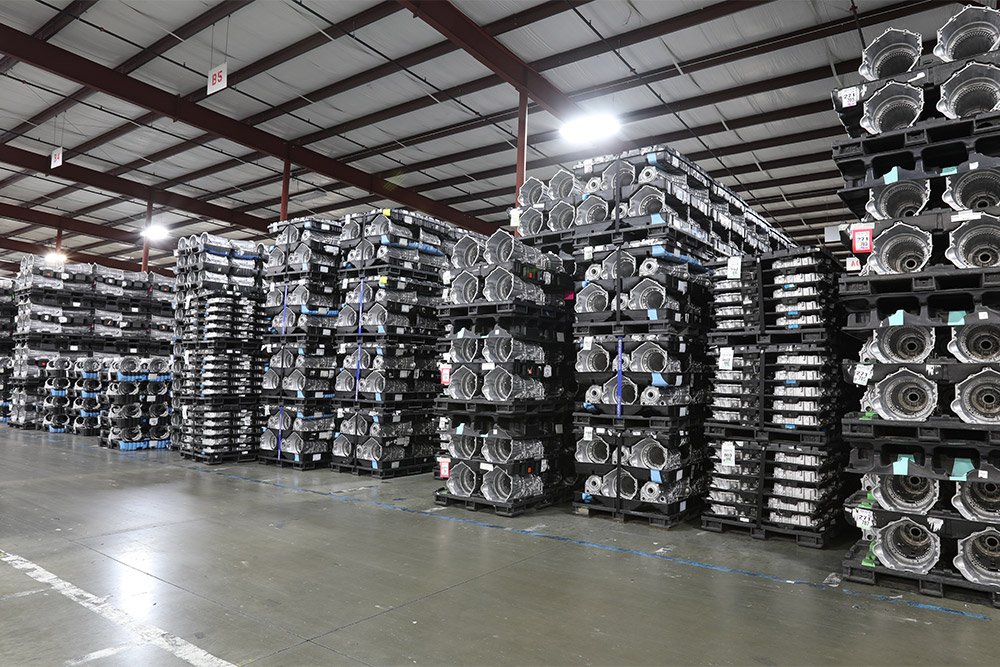
CUSTOMER
CAP Group, Indiana
SCOPE
Design a conveyor solution that increases speed and efficiency for the CAP Group while efficiently moving thousands of transmission casings per day.
END RESULT
Stac partnered with Interoll to design, build and install a Zero Pressure Accumulation Conveyor that seamlessly handles 12,000 transmission casings per day (weighing 43lbs. each) with a 40% increase in speed for an automotive industry supplier. We are proud to provide solutions that increase safety, reliability and greater efficiency for our customers.
FURNITURE MANUFACTURER SELECTS STAC FOR NEW WAREHOUSE STORAGE AND LOGISTICS NEEDS IN GEORGIA.
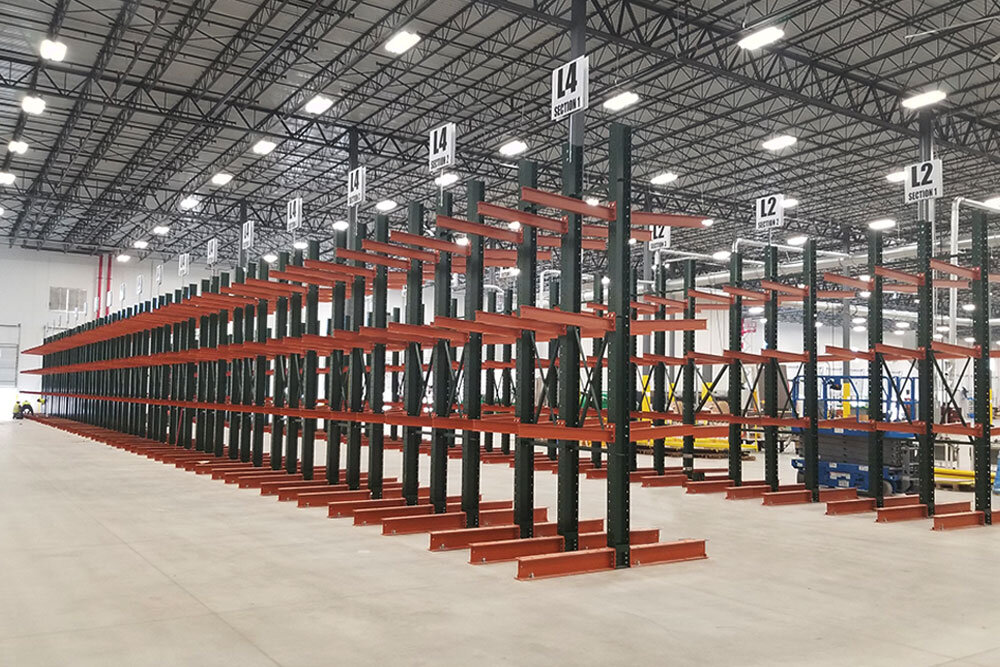
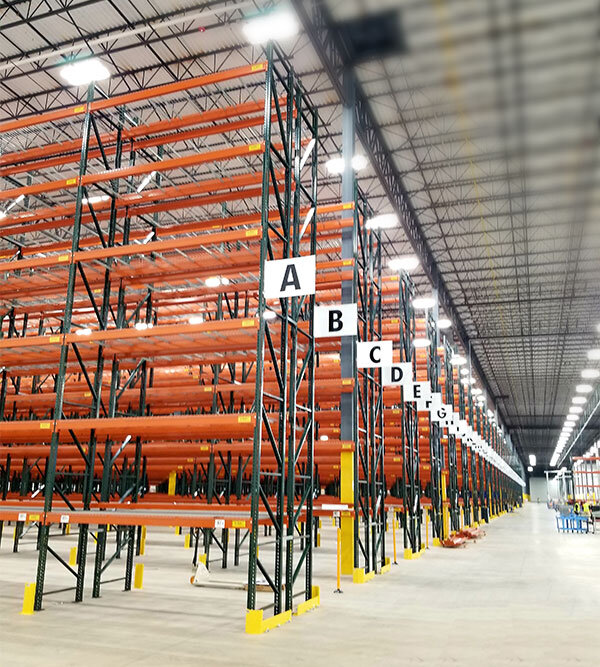
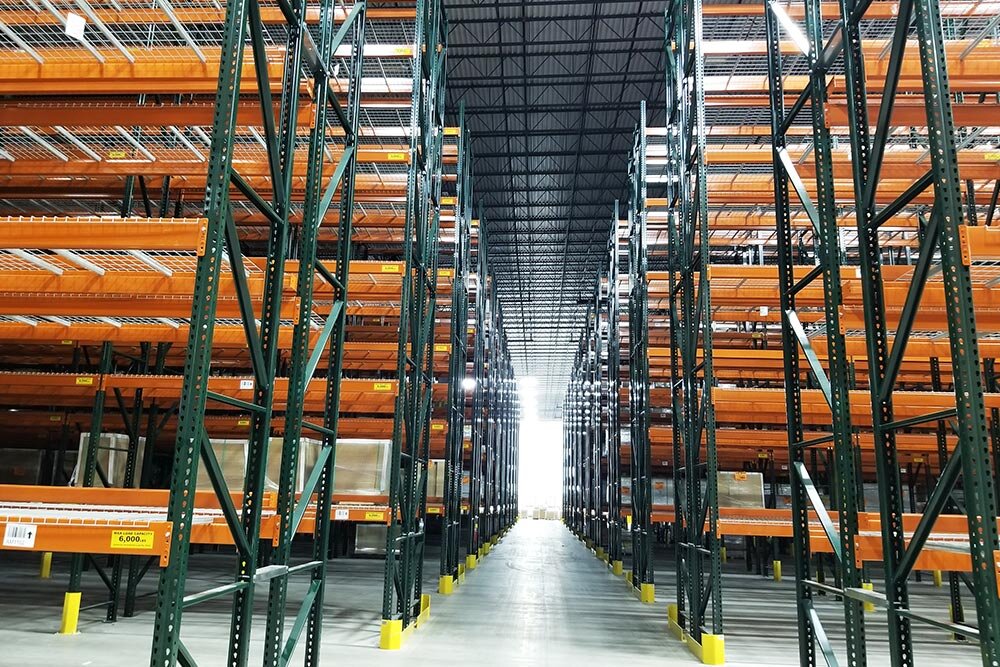
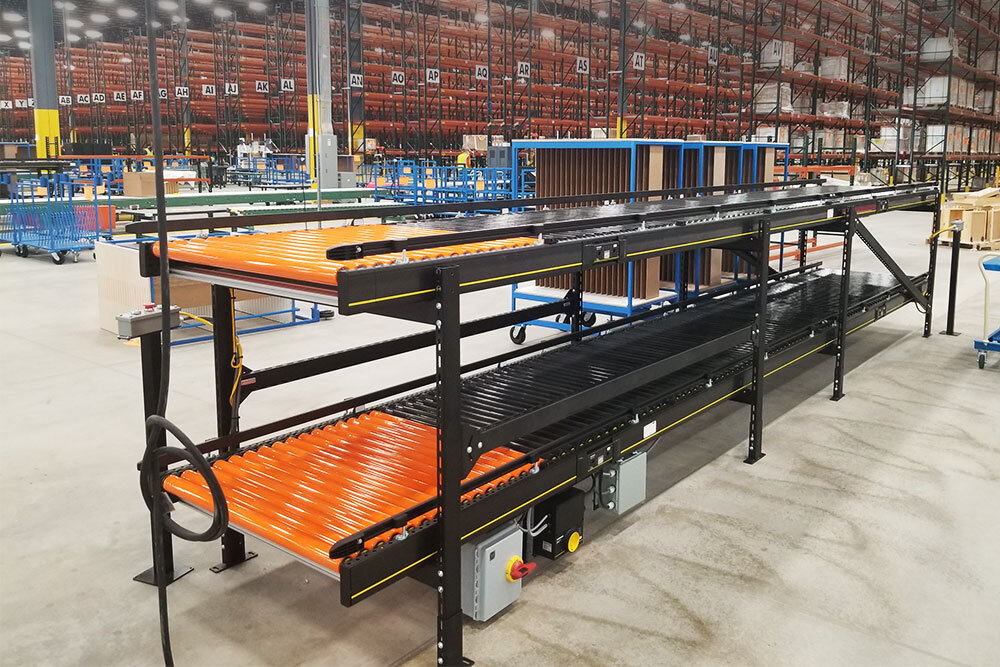
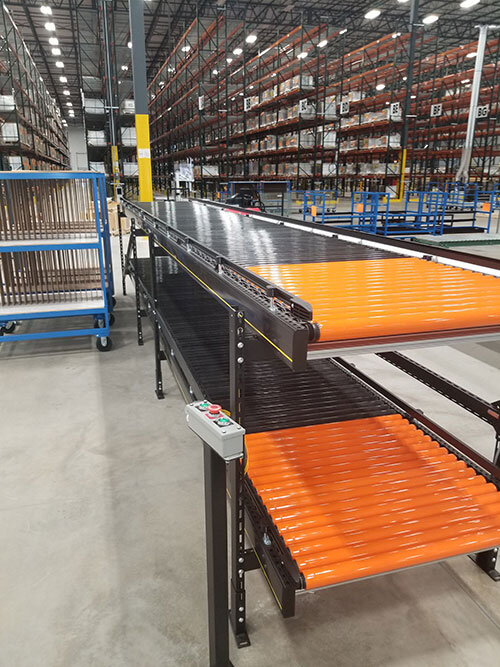
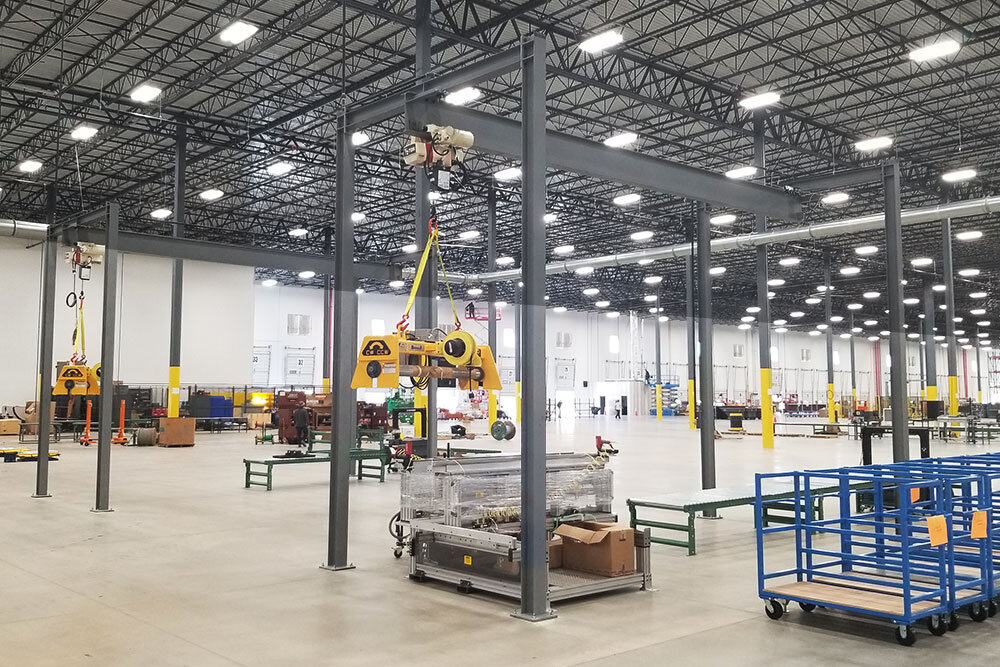
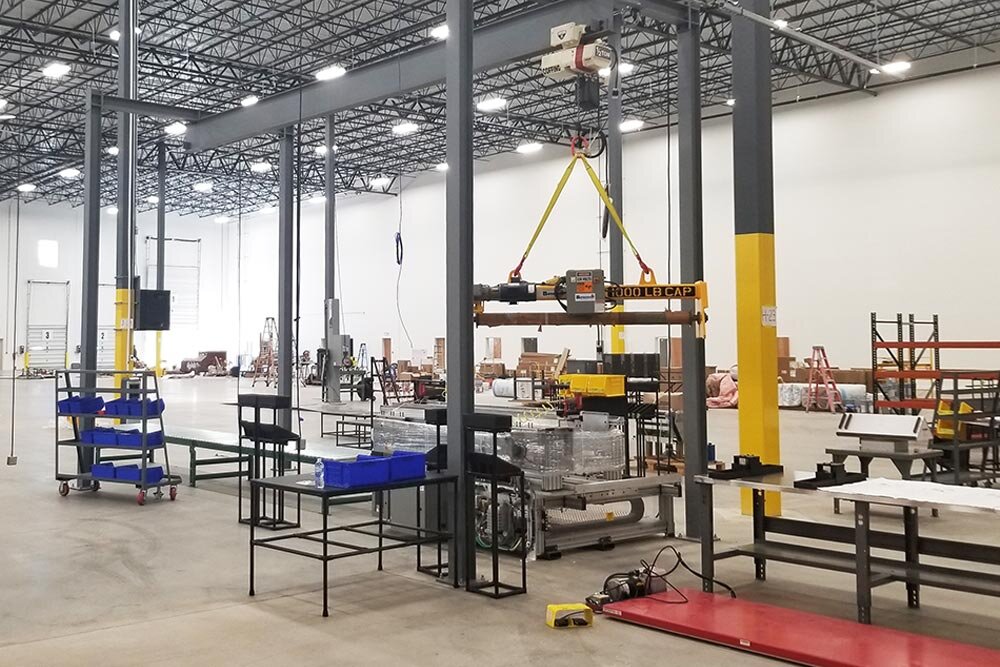
One of the Nation’s largest cabinet manufacturers selected Stac for its material storage and handling needs in the Peach State.
Stac Material Handling worked closely with the customer in designing the layout and working with material requirements documents to ensure a smooth design, build and installation for completion of this $2.1M project.
CUSTOMER
Furniture manufacturer
SCOPE
Design, build and installation of material handling systems
PRODUCTS
Pallet Racking, Cantilever Racking, Accumulation Conveyors, and Crane Systems
THE PROJECT UTILIZED FOUR AREAS OF EXPERTISE WITHIN THE STAC’S CORE CAPABILITIES:
Pallet Racking
- 65 Rows of Pallet Racking Including 1,403 Uprights, 15,168 Beams and 22,752 Wire Decks
- We protected the racking using 254 End of Aisle Rack Guards and 1,149 Post Protectors.
- The design also included 7,584 Bolted Load Stops.
- Over 9,700 Floor Anchors and Floor Shims were used.
Structural Cantilever Racking
- 147 Columns
- 215 Bases
- 657 Arms
- 2 Rows totaling over 250’ long.
Accumulation Conveyors
- 2-Tiered Zoned Drive Roller Conveyor System
- Poly Coated Rollers
- 3-100’ Lines
- 24V DC Drive Motors
Crane System with Hoist
- 2 Half-Ton Free Standing Systems
- 25’ L x 10’ W; 15’ Tall
- 2 Coffing Half-Ton Hoist
METALSA CASE STUDY
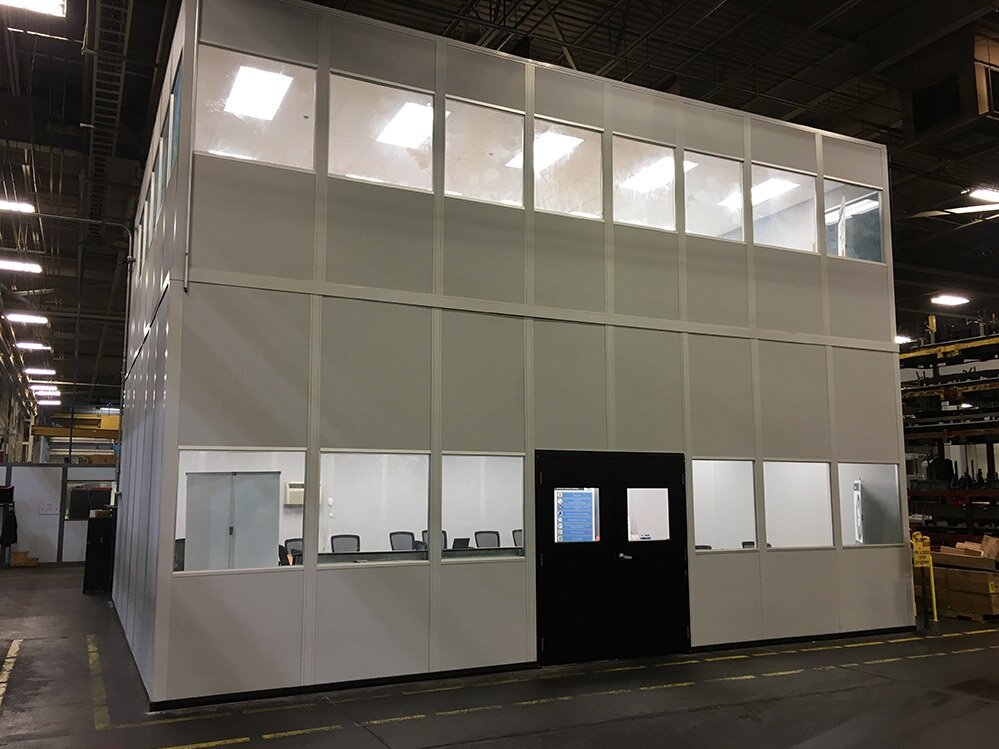
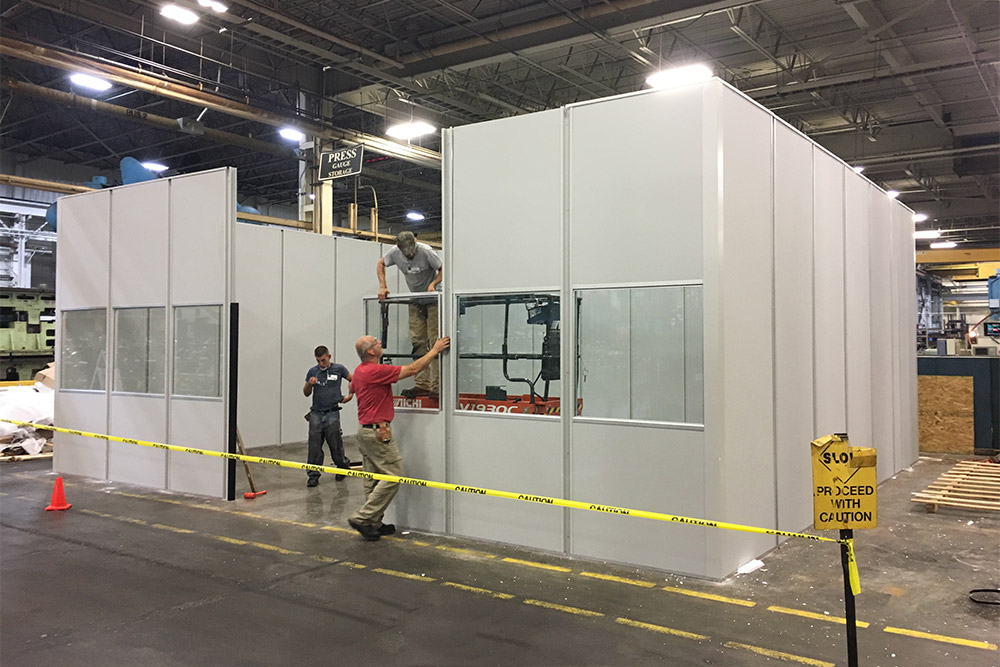
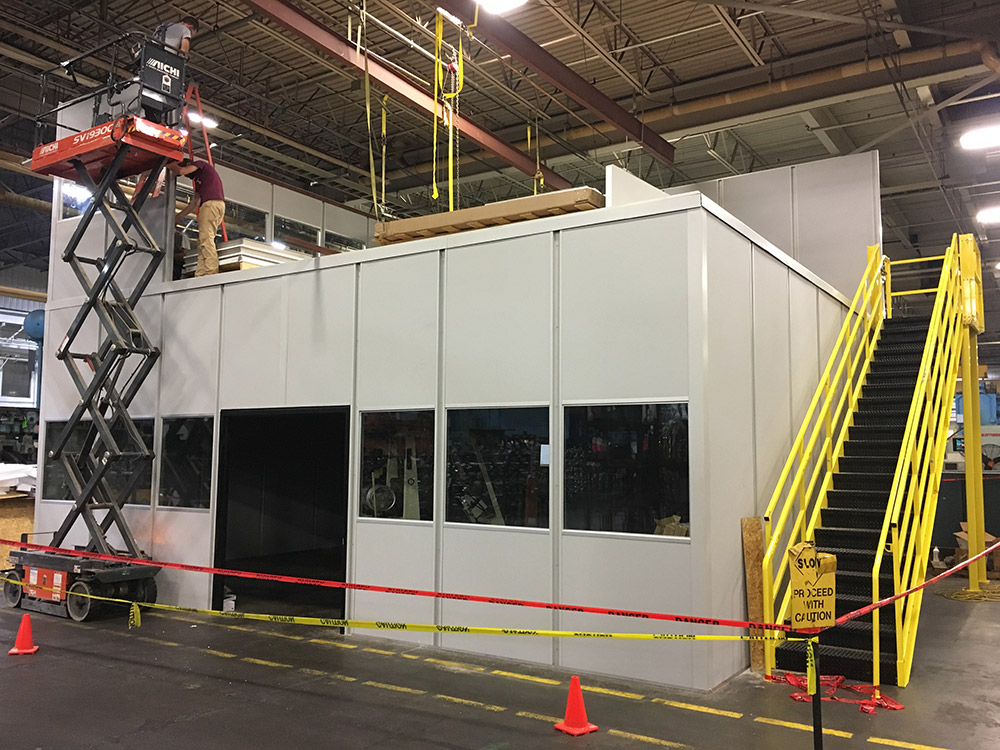
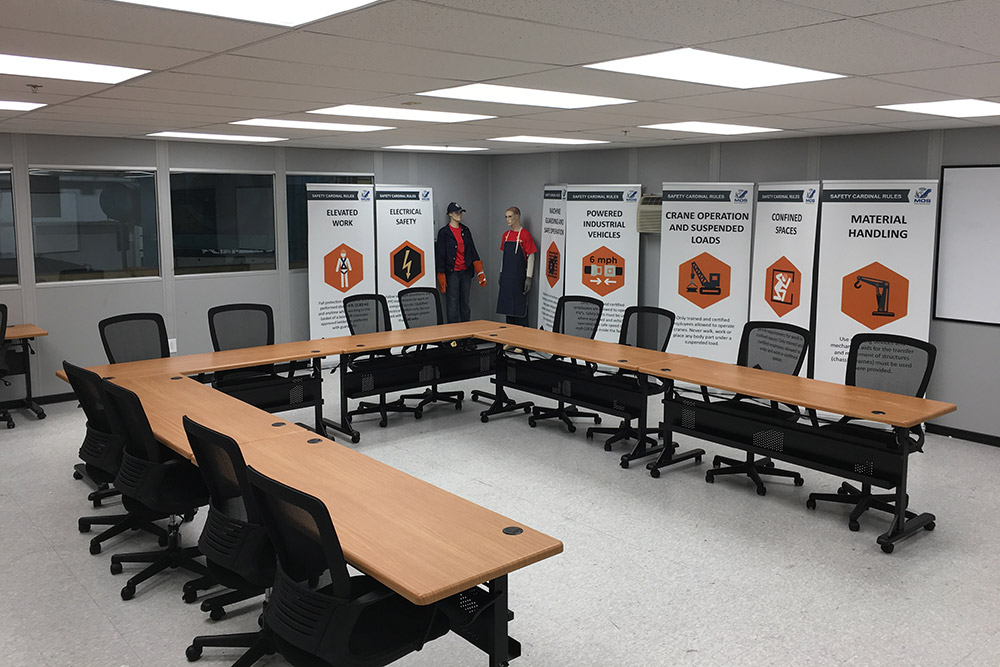
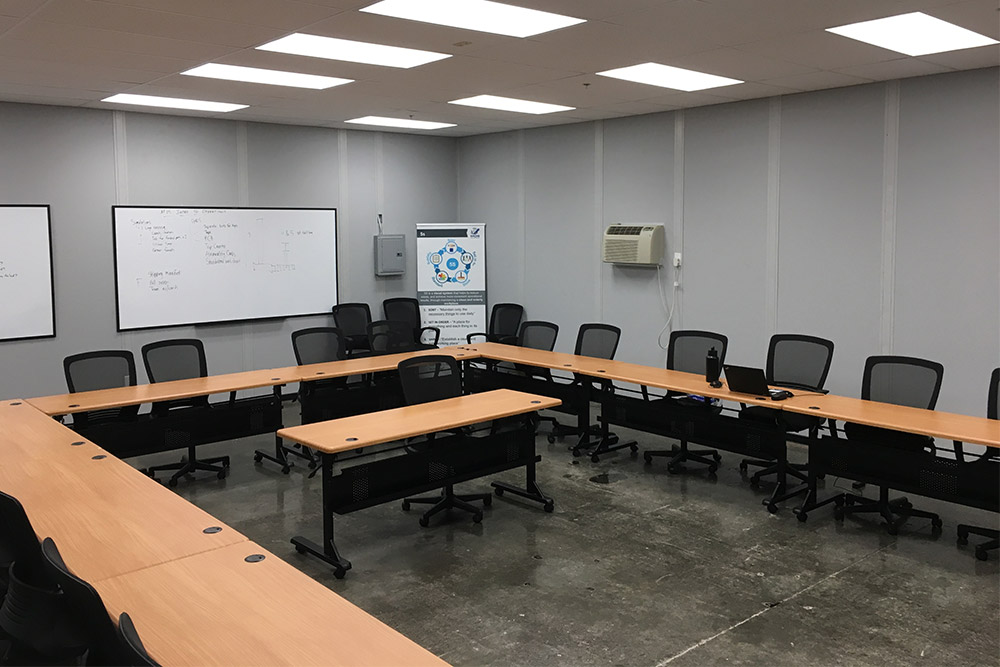
CUSTOMER:
Metalsa
CUSTOMER NEED:
Additional training and meeting space in production facility
Instead of adding on, we constructed 26’ x 30’ two story modular building placed centrally within their manufacturing facility for more office and training space. Metalsa also selected windows in panels for added visibility from the meeting/training spaces.
BENEFITS:
Metalsa was able to add a safety training room on the main level and a conference room on the second level. The facility had no other inside areas that would have allowed them to gain these two types of space that they now can host training for their employees or facilitate meetings. The addition of windows allowed for great visibility to the manufacturing floor. Installation performed by Stac ensured that every need was addressed and the end result was an upgrade to the way the facility is utilized by all employees.
“You and your team have been outstanding with your customer service, which I value the most when it comes to my large capital investment projects I manage at our facility. You guys are great to work with, have the knowledge and understanding already of what we do here, and are quick to respond when it comes to communication.”
— Justin Smith, 80/20
